NextFlex focuses on several hybrid electronic enabled application areas: aerospace, automotive, communications, healthcare, infrastructure, robotics & autonomous systems, wearables, and defense. NextFlex convenes institute members – industry, academia, and government – to collaboratively identify and actively overcome manufacturing challenges in commercializing hybrid electronics-enabled devices, modules, and systems. In addition, NextFlex has a pilot-scale, end-to-end hybrid electronics manufacturing facility – the Technology Hub – where members benefit from process development initiatives for scalable manufacturing, and commercial customers utilize design, prototype, manufacturing, and test services.
NextFlex facilitates the development and manufacturability of hybrid electronics technology that integrates low-cost additive electronics combined with the processing power of thin semiconductor die (integrated circuits - ICs) to create a new category of sometimes stretchable, bendable, conformable, and flexible electronic devices. Hybrid electronics manufacturing relies on additively processed circuit elements, small discrete components, semiconductor die, and application dependent packaging. The low cost, thin size, and light weight of hybrid electronics devices, modules, and systems deliver the long-promised “Internet of Everything.”
NextFlex is advancing the manufacturability of hybrid electronics and driving manufacturing readiness levels toward commercialization, with emphasis on device integration and packaging, flexible components, microfluidics devices, materials, design & modeling, guidelines & standards, final assembly, testing, and reliability. The manufacturing processes at the NextFlex Technology Hub use production-level tools that, in some cases, provide scalable high-yielding advanced processes such as the handling and attachment of ultra-thin die. NextFlex has demonstrated that the hybrid electronics manufacturing process, when compared to traditional printed circuit board assembly (PCBA) manufacturing, reduces the number of process steps by two-thirds. Additionally, the process resulted in the final hybrid electronics based PCBA being only one-third of the weight of a traditional PCBA, creating a path forward for less expensive, faster-to-market electronics.
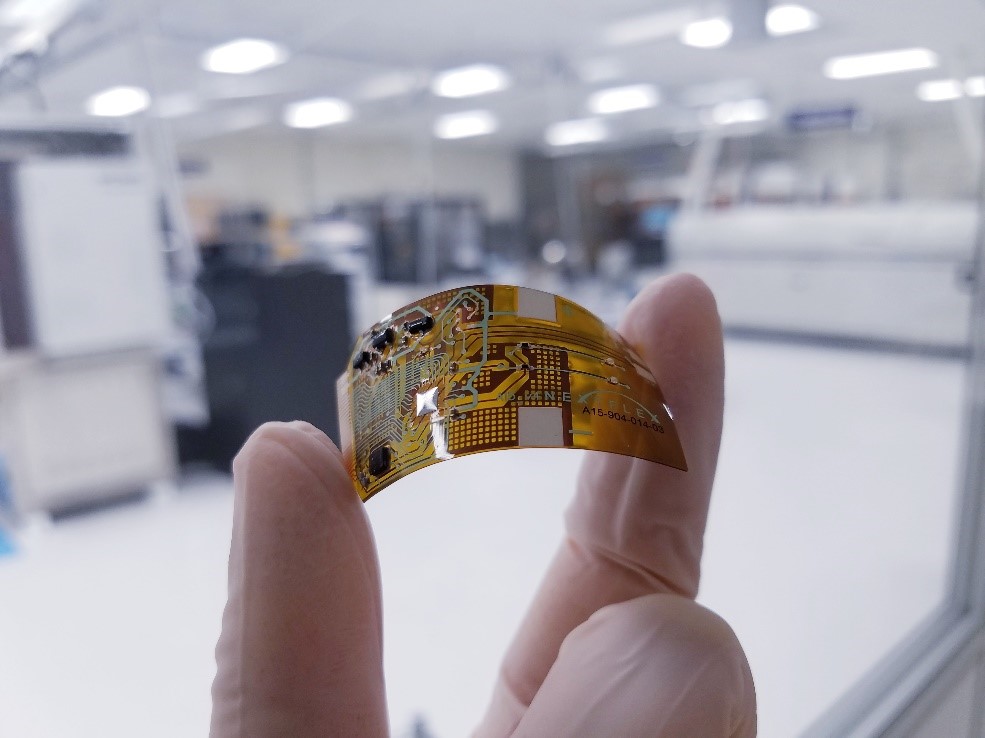